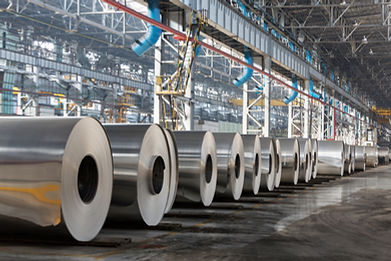
Application
Application of Bone Ash to a surface exposed to molten non-ferrous metals provides a consistent barrier against attack by the molten metals. This property provides the means for the protective barrier.
Dry Bone Ash
is frequently is frequently applied to the surface of refractories in transfer troughs, filter boxes and other vessels which will be exposed to molten non-ferrous metal. A cloth glove or suitable duster is used to apply the dry solids. The bone ash is then rubbed into the pores and packed into the surface of being coated. Best results are obtained when bone ash is applied to new or well cleaned refractories. Difficulties may be encountered when applying bone ash over other coating materials.
Slurry
Bone ash is frequently applied as a slurry. We recommend a starting slurry made by mixing about two pounds of bone ash per gallon of water. Such slurries can be brushed, sprayed or painted on surfaces to obtain the desired protective coating. Surfaces which are painted or sprayed while warm dry quickly. All surfaces must be thoroughly dried before contact with molten metal. Items which benefit from applications of bone ash slurries are dross skimming containers, furnace tools and permanent casting molds. Bone ash coatings not only improve the appearance of the items coated, but also facilitate housekeeping chores.
Slurry Pretreatment
An alternative application method suggested by the aluminum industry begins with a bone ash slurry pretreatment. A slurry is prepared by mixing about two pounds of bone ash per gallon of water. A brush is then used to apply this slurry to clean the refractory surface. When the surface has been wetted and coated with the bone ash slurry, it is allowed to dry. Dry bone ash is then rubbed into the pores of the refractory and the surface packed so that no loose material remains. Subsequent coatings of dry bone ash can be applied without additional slurry treatment.
Coating
Coatings applied as a slurry sometimes flake off. This indicates that the slurry was too thick or that the bone ash slurry did not properly wet the surface. In either case, the flaking can be brushed off and another coating applied using a more dilute slurry.
Packed
Dry Bone ash may be packed into the joints between the refractory sections around dams or other places where reliable, leak proof seals are desired.
Effective
The Aluminum Industry has found bone ash to be particularly effective as a protective material where molten metals are present. Bone ash has proven to be cost effective and a safety advantage when properly applied. Coatings on steel surfaces provide a safety barrier and a "super plus" in overall housekeeping in a casting operation.